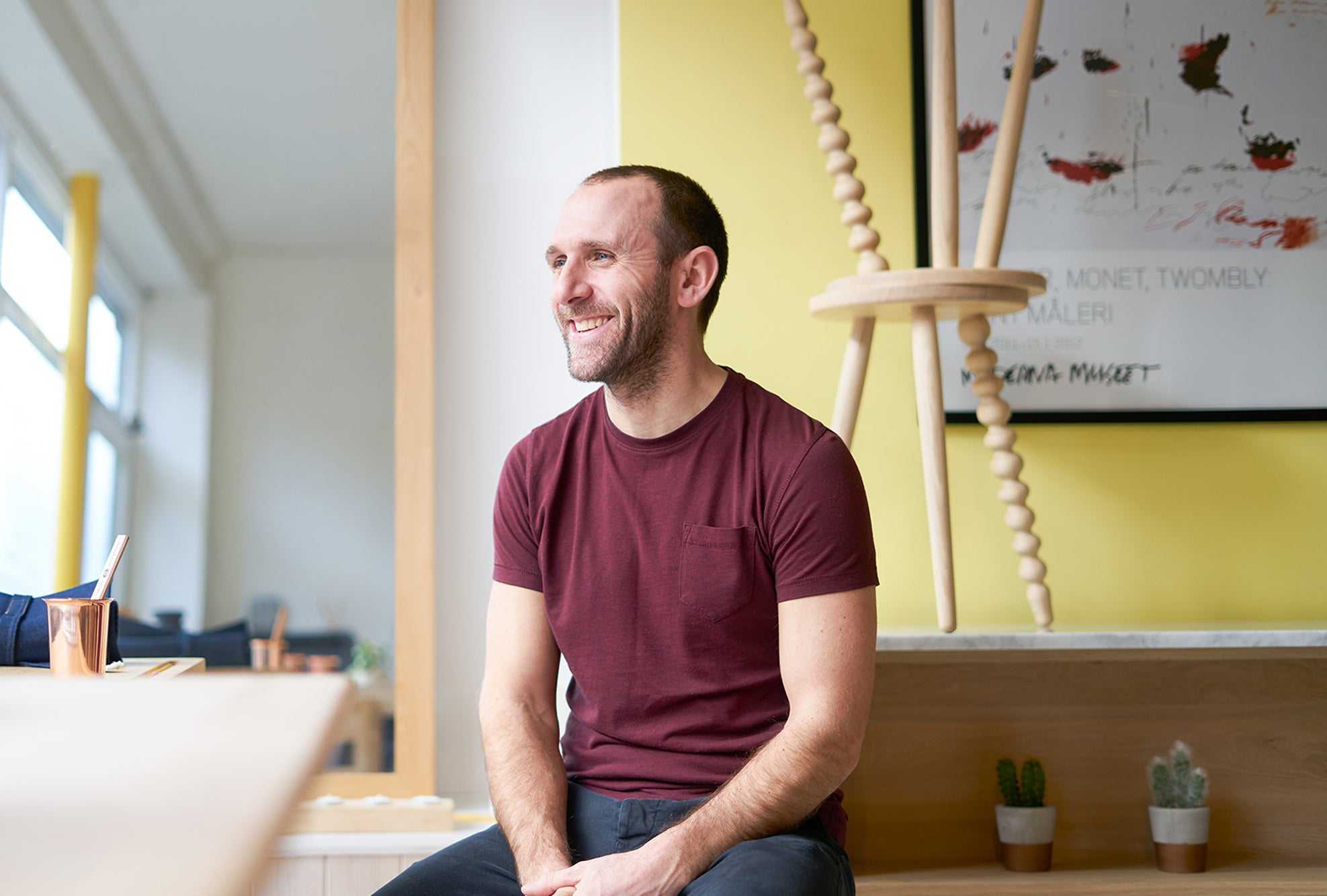
Galvin Brothers
Galvin Brothers is a handcrafted furniture company set up by brothers Matt and Andrew Galvin. Building on their fathers 61 years of joinery and carpentry skills, they design and make handcrafted furniture from their workshop in the East Riding of Yorkshire.
Being a fellow Yorkshireman, also from the same area where Matt and the company are based gives me such optimism about what craftsmanship and manufacturing skills mean in a modern context, especially being a creative business that is thriving outside of London.
I sat down with Matt Galvin at the Galvin Brothers shop in Beverley, East Yorkshire while he was prepping to exhibit at the Maison Objet trade show in Paris. We discussed why he set up the company, how his dad's skills have shaped their manufacturing mentality and what craft means to him.
Full Q&A below.
Matt Galvin Q&A 13/01/19
DH: How did Galvin Brothers start?
MG: When my dad was 14, he woke up one Monday morning and was putting on his school uniform, and my grandad told him “you don't need to put your uniform on, you’re not going to school, I’ve got you an apprenticeship.” He completed an apprenticeship in joinery and subsequently become self-employed, he was a joiner in Beverley for 60 odd years. Even right up to when he died and he was still working in our business and maintaining his own customers at 79 years old, so that was the connection to the joinery.
I studied graphic design at the Royal College of Arts, so graphic design is my trade but even when I was there I used to prefer the product design department, I was obviously a frustrated product designer. After university, I had a successful graphics design career working with some high profile clients such as Paul Smith, who was one of my favourites.
My brother worked for my dad while I was working as a graphic designer in London, I’d travel frequently, staying in hotels, seeing places and different types of furniture and thought, we could make something like that. It also looked like there were patterns emerging in parallel industries; you'd observe the trend for provenance in food and you could see this idea of good quality food translating into other industries such as furniture. Almost like an antidote to mass production, I saw the possibilities of what we had in house: craft, talent, understanding of materials and with me being a designer, it felt like a natural opportunity.
We thought we'd give it a go and see what happens, starting in February 2012, the original plan was to get my brother going earning £500 a week and stop him wasting my dads time and then I’d go back to London but I never went back, that was 6 years ago. Never been in retail, never been in furniture. It’s amazing what transferable skills you have from being a graphic designer.
One thing lead to another and we had an amazing first year, being nominated for a British Design Award for the ‘Perfectly Imperfect Stool’. We gained momentum rapidly, so before I knew it I was only thinking about this business and not my other.
DH: So for a while, you were doing both?
MG: Yes, I was servicing all of my graphic design clients in London for a while and then didn't really go back.
One the biggest questions that people ask me is that I must miss London, but as 80% of our clientele is based in London, most of our orders go there, the interior designers that we're working with are based there, I still have a strong relationship with London. There are things you miss about the city but I realised that as long as I'm being productive. I don't care where I am but I only feel at home if I'm being productive.
DH: Tell us about your dad and brother, did you want to create something to utilise their carpentry skills?
MG: Yes, absolutely. My dad and brother were working and earning an honest wage, and I used to look at their skill set and think you're undervaluing yourself. My dad never charged more than £18 an hour and some of the things he was making were seriously complex and very clever, not only in working out how to do them but physically making them too.
When we grew up my dad always had a workshop in our garden, we always had a property that had a reasonably sized piece of land that he would always put the workshop on and growing up in and around that, although I didn't know it at the time, I was gaining an ingrained understanding of materials, particularly timber obviously, proportion and some processes, which was more natural now I think about it than the graphic design.
So the process of making was easy for us as we could rapidly prototype furniture, making it right there in the workshop. We go from a sketch like most product designers but they would then have to develop that and make a model of the next prototype or a digital model, take it somewhere where they will fabricate it and you go through this prototyping process. We would just make it and refine it until we see it.
DH: That's a huge benefit having the workshop on your doorstep in Yorkshire and the ability to do a sketch, make it and develop it instantly.
MG: Yes, for example, we would turn a leg for stool and then review it, talk about how it needs to be a bit thinner there, a bit fatter there and we would do it instantly. When we did our wobbly leg stool, we did two or three versions of it, working to get the proportion right and then let it be. Our refining process is kind of back and forth, but because it's in house, it's almost symbiotic in a weird way, It's just all mixed into one which seems to work for us.
DH: Where did the 'perfectly imperfect' leg detail come from?
MG: It was quite random, I was actually thinking about it recently because it’s six years on now. We were developing an archetypal stool, with the three legs that we had already made, our pippy oak stool and it was just a bit of whimsy, a funny little drawing, and some playful disruption. I’d drawn the wobbly leg so many times, I can't find the original drawing but there was definitely one on a napkin and then there's been lots on scraps of paper and the back of invoices.
It’s perfectly imperfect because one of its legs is different from the others but every one of these bobbles, its ups and it's downs and the spacing are all wrong. We would do it wrong on purpose until it felt right and aesthetically quite pleasing.. and obviously, it’s phallic which is its big sell!
DH: What does craftsmanship mean to you and Galvin Brothers?
MG: For me, it's the quality of the product we make being truly of a high standard. Craft has become a bit of a buzzword. Luxury goods have always been crafted beautifully but the craft was about was a detail, then manufacturing it in a way that is the best for the product, not just subservient to aesthetic. If you go to an amazing shoemaker, they will not compromise the quality of the leather, the quality of the stitch or the way the sole is stitched to the upper, no matter what. They push the limits of that around the aesthetic and it’s exactly the same for us in the furniture.
If you're working with a joiner, cabinetmaker or a carpenter, particularly Pascal, our lead joiner, I can show him a drawing and there's a point where he'll just say “no, we can't make it like that because the joint will be too weak”, so we change the design or think of a way of joining it differently or it has to have an undercarriage. There is a point where the craft element means that the design cannot compromise the integrity of the piece. Pascal has had one of the most traditional educations in his craft, he's invested in his knowledge and skills so he won't compromise it for the sake of a design, then these two things get pushed together and this is really where the craft is important because it goes beyond the idea.
We’re making something that is built to last, hoping the product is going to last beyond our lifetime and I think, along with the pride in making it, it’s a good business strategy for us. We’ve genuinely only had one return in six years and that was for a different reason! The only time something comes back to us is when it’s broken in transit. We may get the occasional problem with the timber, as it’s a natural product, sometimes difficult to work with as it moves, twists and changes or it might have knots or crack in it that we may not have seen during manufacturing process but we resolve these problems because that is the craft, you don't make something that isn't made correctly.
DH: So it sounds like craftmanship to you is not compromising on quality and keeping the integrity of the materials.
MG: Yes, I put a put something on the Instagram a few months ago “there's a difference between knowing how something is done and knowing how to do it, the latter requires dexterity and wit.”
Knowledge is also crucial if you take Pascal or my dad, they started with their apprenticeships. Seven years as an apprentice was just the basics and they knew to get to the end of that seven years that you don't know everything, you are just seven years further in learning for the rest of your life. Craft is something that is so cumulative is unbelievable, even the minutiae of oiling tables and benches, I know how we finish our products as we've been doing it for six years and you’re learning tricks all the time. Every time I go into the workshop and we're finishing another job, you pick up other things. Pascal has 30 years of that cumulative knowledge and he doesn't think he's done, he’s still constantly learning and thinking of ways around challenges.
DH: I read you are very particular about where your timber comes from. So you are mindful about sustainability, how important it is where it comes from and the sustainability of the timber?
MG: It’s twofold really, a resource like wood is a finite resource and connected to our very existence on the planet, it’d be foolish to chop trees down with no care for what for that is, so from a moral and ethical point of view we’re engaged with the idea that we need to take timber from sustainable sources. That's critically aligned with the quality of the product that you make. There are varying qualities in timber, some of that is to do with the speed in which the tree was grown, the care in which was taken in order to farm that product, how it was felled, planked, and the speed at which it was dried. All of these things, if not done correctly will compromise the quality of that resource.
If you buy cheaper timber where these processes haven’t been done correctly, you waste more timber in the process, as some have to be discarded because it's structural integrity is compromised, you’re then being more wasteful, both with the resource and your money. It doesn’t make sense for a furniture manufacturer who makes things in wood, to be wasteful in wood as you’re just turning money into expensive sawdust and burning it in your wood burner. It's all connected with the idea of being sustainable as a business, if you aren't, then you're probably wasting money.
DH: If you're unsustainable, you are probably not a good business.
MG: Yes, exactly. It's a no brainer. In the short term, you may have to spend a little bit more but in the long term, you're going to be saving money. Notwithstanding wages, our biggest expense is timber, our raw material, so we just get a good one and it means we will waste less in the process and the quality of the product is better.
We are constantly looking for ways to utilise the waste, we do a large consignment of furniture in English ash and because of the design of the furniture and the varied nature in colour of the timber, there’s some natural waste from it. From the offcuts in the same boule of timber, we can make other things and with smaller bits and sawdust we burn to heat our workshop, which is an appropriate thing to do and it's also cheaper and more sustainable than electricity.
DH: How would you describe your products?
MG: It's hard for me to describe. I think in some ways it's for other people to describe them.
It’s like one man's musings, not that it’s just one man but we are a handcrafted furniture company and we just make our whimsy. We make what we fancy and think someone else might fancy it too. It's always better when it's made in that way. If I observe the market or if I try and think about what people might want, you tend to end up with things that you're not that excited by.
DH: From a design perspective, looking into the shop, you can see there's a common thread running through the whole design, so obviously has an aesthetic from a design point of view that is Galvin Brothers.
DH: What are the future plans for Galvin Brothers?
MG: We're doing an increasing amount on the interior side of things, which is exciting. My partner Stacey is an interior designer and were looking at setting up spaces in Beverley and London, where we can showcase our products and really art direct the space, our aim is to make the spaces multi-use; part bnb, part showroom, part customer experience and part brand experience. It will give customers the opportunity to get close to our products and bring them into a space we have created. It also gives us the chance to road test new product developments and refine them further if needed. I think it will bring new opportunities and design too, a direct response from creating an environment that is a domestic setting rather than for a retail space.
Galvin Brothers' beautiful products are available on their website and from their store.
Beverley
East Yorkshire
HU17 ONP